|
The oldest and still the most common industrial thermometer is the thermocouple. Its origin can be traced back to Thomas Seebecks 1822 report of the Seebeck effect. The correct definition of the Seebeck effect is that a difference of potential will occur if a homogeneous material having mobile charges has a different temperature at each measurement contact.
This definition is different from the one you find in most publications. Seebeck's original experiment was with a single homogeneous conductor. He noted that a voltage difference appeared when the wire was heated at one end. Regardless of temperature, if both ends were at the same temperature there was no voltage. If the circuit were completed with wire made of the same material there was no current flow. (see Figure 1)
The thermoelectric voltage resulting from the temperature difference from one end of the wire to the other is actually the sum of all the voltage differences along the wire from end to end:
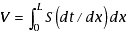 |
(1) |
where:
S = Seebeck coefficient in µV/°C
As long as the thermocouple wires remain homogeneous, the temperature difference between the endpoints; determines the net effect of the summation of all the infinitesimal voltages developed across the infinitesimal distances resulting from the temperature gradient. The Seebeck coefficient of a particular wire material is the first derivative of the thermoelectric voltage as a function of temperature in other words, the difference in potential that results from a difference in temperature. Unfortunately, the Seebeck coefficient is not a constant but instead varies with temperature. The Seebeck coefficient for Type K thermocouples, for example, drops rapidly below 40°C, where it is ~36 µV/°C, to 17.8 µV/°C at 190°C. It peaks at ~630°C at 42 µV/°C.
Thermocouples can be made from a variety of metals and cover a temperature range of 200°C to 1800°C. Advances in metallurgy have made the production of high-purity thermocouple material more reliable than in the past. Comparisons of thermocouples to other types of sensors should be made in terms of the tolerance given in ASTM E 230 or product data.
|
|
Thermocouples have three really significant advantages:
 |
They are capable of being used to directly measure temperatures as high as 1800°C. |
|
|
 |
The thermocouple junction may be grounded and brought into direct contact with the material being measured. |
|
|
 |
They can be very rugged. Thermocouples are frequently made of swaged thermocouple wire by a process that entails drawing the steel sheath and the thermocouple wires while at the same time crushing and compacting the internal ceramic insulation. They are also made by inserting an assembly consisting of thermocouple wires threaded through ceramic beads into a steel, Inconel, or ceramic sheath. Beaded construction is most common for the higher temperatures. |
That's about the end of the advantages. Here are a few disadvantages:
 |
Every temperature measurement made with a thermocouple requires that two temperatures be measured, the junction at the work end (usually called the hot junction) and the junction formed when the thermocouple wires meet the instrumentation (copper) wires (cold junction).
There are actually two cold junctions formed at the measuring instrument. The positive thermocouple lead and one of the copper leads form one junction and the negative thermocouple lead and the other copper lead form the second. Both junctions are considered to be at the same temperature, and, if that is the case, there is no additional error introduced by the copper wires of the measuring instrument.
In the past, the cold junction was held at 0°C by actually placing the wires in an ice bath or by the use of an electronic thermocouple reference junction. Today, most electronic instruments measure the temperature at the terminal block using a semiconductor, thermistor, or RTD and digitally adding in the additional voltage that would have existed at the terminal block if it had been at 0°C. |
|
|
 |
Thermocouples may appear simple but their operation is complex, with many potential sources of error. The fact that the thermoelectric voltage is developed along the entire length of the thermocouple wires explains the reason that loss of homogeneity, which may result from corrosion occurring anywhere along the length of the thermocouple wire, will introduce error. |
|
|
 |
The materials of which thermocouple wires are made are not inert. They are subject to instability resulting from a variety of factors such as the atmosphere to which they are exposed and the rearrangement of their molecular structure resulting from temperature exposure. |
|
|
 |
Thermocouple-measuring circuits must not draw current. The wire has much higher resistivity than copper, and despite the fact that a short circuit exists at the hot junction, by the time it reaches the measuring instrument it can become an effective antenna for radiated interference (EMI). |
|
|
 |
If there is significant distance between the point in the process where the temperature measurement must be made and the electronic measuring instrument, the cost of the thermocouple wire connecting the two may become an important consideration. |
|
|
 |
The relationship between the thermocouple millivolt signal and the process temperature is not linear. Because of the availability of microprocessor-based measuring instrumentation, this is much less a factor today than it was in the past. The equations representing thermocouples are polynomials consisting of constants to 10 decimal places with temperatures raised to the 23rd power. |
|
|
 |
When time response requirements require that the thermocouple junction be grounded, an isolated signal conditioner is essential to prevent the ground loop that would result from a direct connection. |
For many industrial measurements the thermocouple is the only cost-effective solution but if accuracy and stability are required, the calibration of the installed sensors must be checked frequently. This calibration should be carried out while the thermocouple is in use by comparing it to a nearby comparison thermocouple. If the thermocouple is removed and placed in a calibration bath, the output integrated over the length is not reproduced exactly and it must be assumed that the thermocouple is still homogeneous. Since this is an unlikely situation, it must be concluded that this type of calibration is flawed and if accuracy is important, the thermocouples should be replaced routinely.
|